Retech Receives Purchase Orders for Two High-Volume Plasma Gas Atomizers
Feb 08,2024
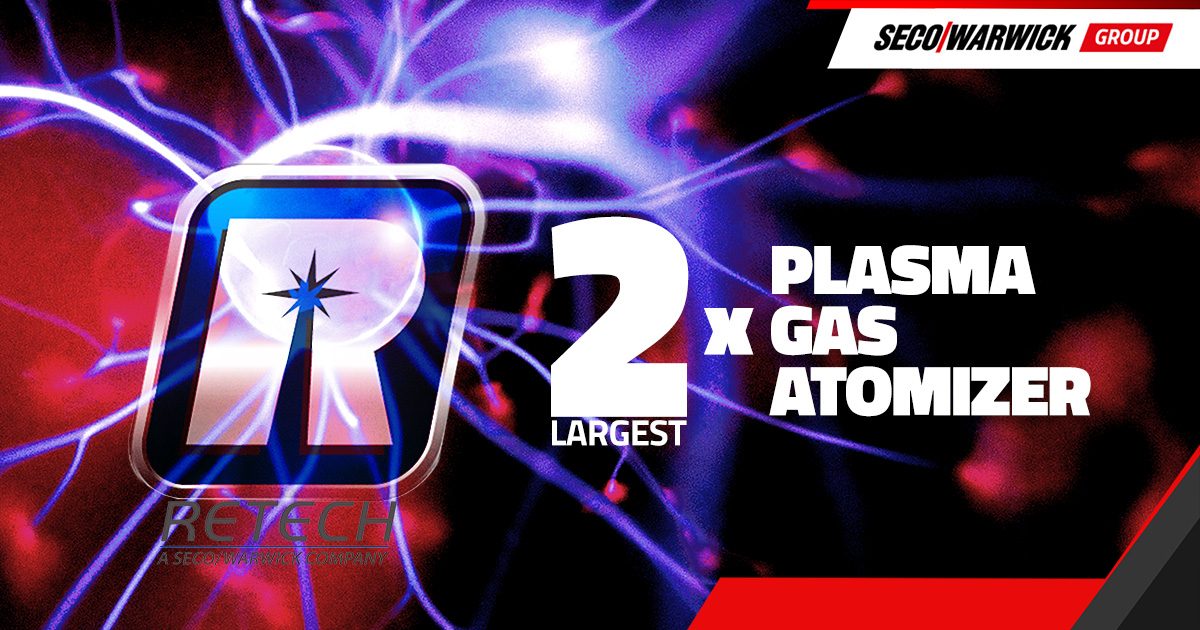
Slated for use in a proprietary technology, the destination and application are under wraps, but the versatility and capacity of Retech’s PGA300 means that they could be put to use atomizing any of a wide variety of refractory and reactive alloys, amorphous metal, or superalloys, and do so at production rates that will redefine powder metallurgy industry expectations.
Alternate powder production technologies each run up against limiting factors when trying to scale up the process. Retech has developed an atomizer die technology that can achieve far greater atomization rates compared to competing technologies. The PGA 300 can atomize titanium at rates exceeding 1500 kg/hour! Paired with the reliability and versatility of plasma melting, the PGA uses a versatile feedstock process to allow for any feed formats suitable for plasma hearth melting, which include loose sponge, compacts, scrap, and ingots. Elemental feed can also be used, and alloying can occur directly in the hearth during the melting process. Paired with material feeders, this turns the operation of the PGA into a semi-continuous process that only pauses for melting of a fresh charge, rather than having to open the furnace and restart the whole process every time the feedstock is consumed.
“I would say that the PGA 300 is our largest offering today, but the benefit of this platform is that we can further scale this technology. We have installed larger plasma melting equipment for our customers and we want to utilize this proven technology to continue to scale the PGA platform” – said Earl Good, Retech Managing Director.
Retech’s advances in atomization dies also allow for a narrower Powder Size Distribution (PSD), and a better d50 average powder size selectability than alternative powder production methods. Exact PSD, d50, and rates differ depending on the alloy.
With a production capacity of a thousand tons per year, the PGA300 may be the largest high temperature alloy atomizer Retech has built so far, but their experience indicates that the scalability is only limited by a customer’s demand, finally taking inert-atmosphere powder production to a truly industrial scale.