SECO/WARWICK Develops Single Crystal Casting Technology for the Aerospace Industry
Jul 09,2025
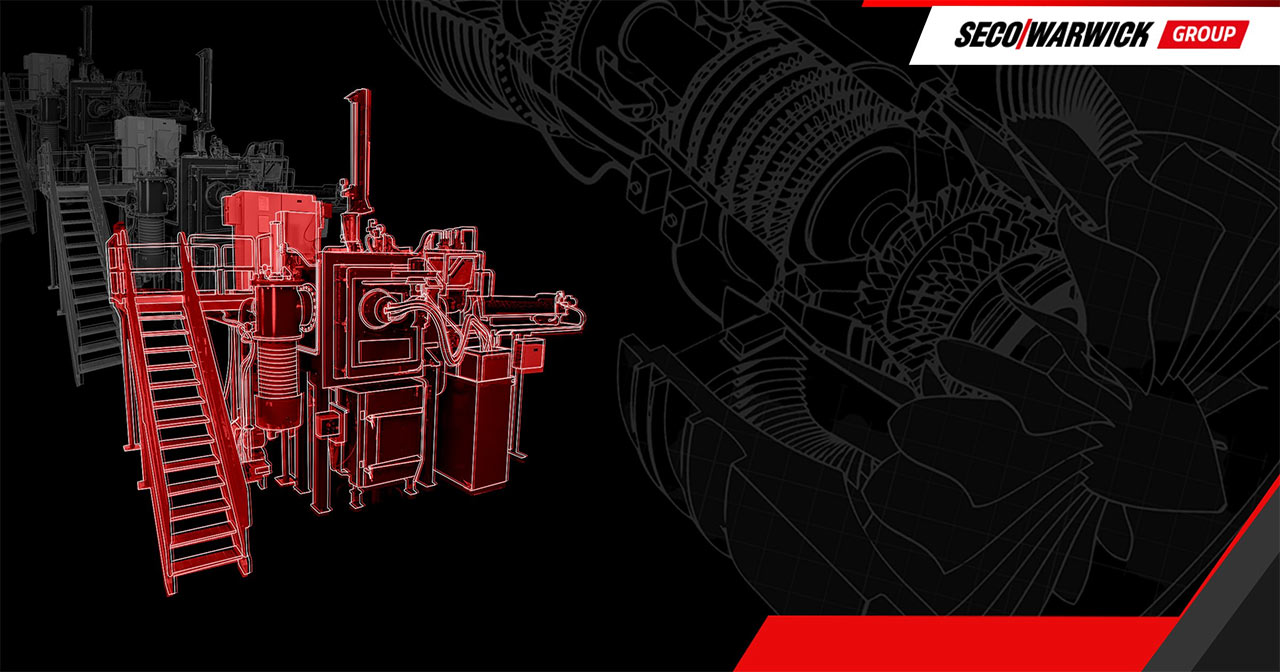
SECO/WARWICK successfully implements VIM technology for an industrial foundry specializing in the production of parts for the aerospace industry. For one of its European partners, SECO/WARWICK will deliver 3 induction vacuum melting furnaces for casting using directional solidification or single crystal methods.
This partner already has 7 VIM units in its production facilities. VIM technology opens up new possibilities for single crystal casting of nickel and cobalt superalloys.
“This is a returning partner who will now have a total of 10 VIM units of our brand. In the VIM DS/CS furnace, the client can obtain castings using Directional Solidification or Single Crystal technology. The well-designed furnace structure, with the highest quality materials and components, as well as a state-of-the-art control system, allows the user to produce the highest quality castings,” said Sławomir Woźniak, CEO of the SECO/WARWICK Group.
VIM produces the highest quality in casting
The VIM furnaces on order have a maximum capacity of 40kg. These are vacuum units with induction heating, in which DS/SC castings can be obtained.
The popularity of VIM furnaces and the growing importance of vacuum metallurgy is partly a consequence of the continuously changing production needs of aviation. The most modern jet engines utilize advanced blades cast using single crystal technology. The user-friendly control system ensures precise processes: casting, temperature control, and comprehensive data collection. SECO/WARWICK VIM furnaces are equipped with unique and intuitive control systems that provide the repeatability of results and unrivaled throughput so important for the aviation industry.
SECO/MELT – Get to know the VIM furnace
SECO/WARWICK’s R&D center is equipped with an induction melting furnace for vacuum metallurgy. The furnace enables the production of Equiax (EQ) castings, as well as using Directional Solidification (DS) and Single Crystal (SC) Bridgman Method technology.
“We help companies that are starting their adventure with vacuum metallurgy and those that need confirmation of the possibility of applying the selected technology for specific details. The client also has the opportunity to get to know the device and participate during the process,” commented Łukasz Piechowicz, R&D Director of SECO/WARWICK.